There are several ways in which companies can act now to fine-tune their approach to turbine maintenance in a way that makes a tangible impact on the bottom line. The most prevalent of these, currently, is using “Industry 4.0” technology.
With connected sensors throughout each turbine, operators can monitor loads, stress levels and operating conditions in real time. Combined with advanced AI-led data analytics, this allows engineers to not only spot problems before they occur, but also to use predictive maintenance across the entire enterprise, minimizing downtime and maximizing output.
As the economics of wind energy continue to face more pressures, digital technology applications could unlock significant value for industry participants across the entire supply chain.
Daniel Fraile, head of market intelligence at WindEurope, points out that although digital technology applications could unlock significant value for industry participants, we are still a ways away from widespread uptake:
“Today, manufacturers and operators are sitting on vast banks of data that are never seen, let alone analyzed or optimized. For instance, a typical onshore wind farm can generate about 500 TB of data every 13 days. At a moderate operating load and 20-year lifetime, this would translate into more than 61,000 TB for a single site.
Engineers will select just a few indicators to monitor in real-time and monitor other indicators at semi-regular intervals. But much of the collected data will never be consulted until a failure occurs. Many operators do not adopt more sophisticated data analysis tools or digital solutions because of upfront costs, time or a lack of knowledge on where to start.
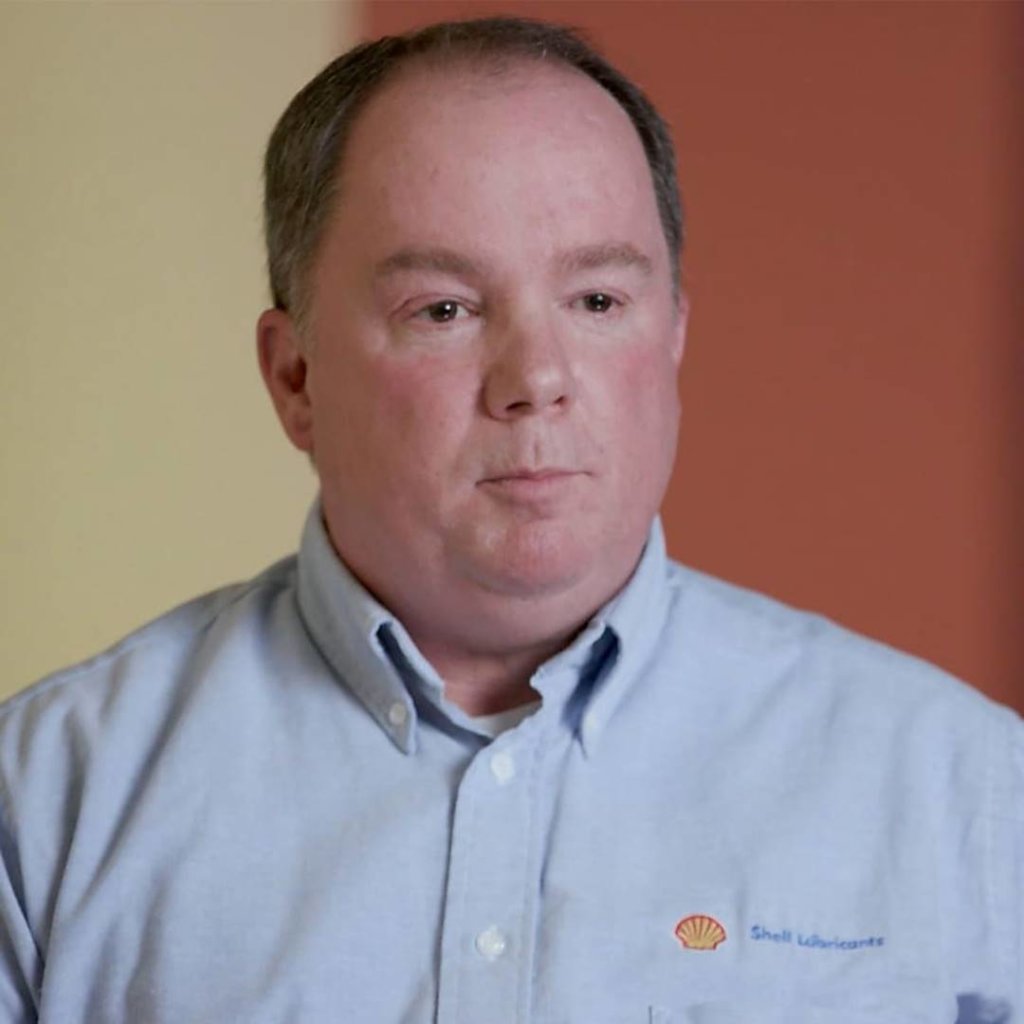
The value of data analysis seems to become even more apparent when wind farms approach the end of support schemes and end of their expected lifetime. Over the next decade, between 40 GW and 60 GW of wind energy will reach the end of its designed operational life, according to the latest WindEurope estimates.
But some of these assets will be fit to continue safe operation beyond this time, and digital solutions could play an increasing role in addressing lifetime management strategies for wind turbines.
For example, creating digital ‘twins’ for prognosis of failures in key components would help operators to decide how long they should ‘sweat the asset’ (operate it without maintenance interventions) and decide at what point maintenance, overhaul and replacement of components will yield maximum benefit.”
To achieve the maximum benefit from these technologies, it is important to consider how they will impact each other, as well as how they will impact elements of your current maintenance regime. The best way to do this is to work with specialist providers that are able to partner with your engineers and scientists – including, where appropriate, by providing training – to analyze your needs and identify the right approach and the right products for your business.
A dynamic in which the need to optimize operational and maintenance costs repeatedly loses out to other issues has created an odd state of affairs. Power generation companies know that operational optimization is an issue that will have a significant impact on their bottom line and long-term sustainability. But, in many cases, companies are not yet acting on that knowledge.
By taking a total cost of ownership (TCO) approach to operations, companies can significantly reduce their running costs. By looking at the full picture when purchasing or maintaining equipment and/or operations, it allows decisions to be made based on cost-efficient output, rather than short-sighted, up-front costs.
A 2017 study by Accenture, “New Value Prospects: The Future of Onshore Wind Operations and Maintenance,” found that operators that streamlined their operation and maintenance practices reduced their overall running costs by 30%. Operators who move toward a holistic approach to maintenance will be well placed to gain a competitive edge over their competitors. This will help not only with the immediate bottom line, but also in making sure they are strategically placed for the next round of public investment in wind power.
Some of Shell’s recent research found that 84% of executives in power companies recognized that effective equipment lubrication can generate savings and have a significant impact on the bottom line. Despite this, there appears to be a gap between intention and action, with over one third (38%) saying that lubrication is rarely a priority. And as a result, 40% say their companies still experience regular breakdowns because of ineffective lubrication.
A key reason for this appears to be a lack of training and understanding of the benefits effective lubrication can bring to equipment, with 83% thinking maintenance staff would benefit from additional training in the theory and practice of effective lubrication.
High-quality lubricants and greases, when effectively managed, have the ability to help improve equipment productivity and reduce unplanned downtime. They protect the heart of the wind turbine (the gearbox), and the strong thermal stability of synthetic lubricants allows them to optimally protect equipment in the extreme temperatures faced. By minimizing deposit wear and ultimately friction, wind turbines can run smoothly, contributing to extended equipment life.
The oil life of lubricants varies from product to product and can also play a big part in effective equipment maintenance. For example, the 10-year oil life of Shell’s Omala S5 Wind reduces the number of oil changes for operators by 33% over a 20-year lifespan when compared to a conventional synthetic wind turbine gear lubricant. Choosing a lubricant that offers oil-life benefits such as this allows reduction in equipment downtime and costs associated with oil changes.
Collaboration will be key to unlocking success in the wind industry. Working with third-party experts allows you to deploy field specialists where needed to find the right technical and organizational approach to challenges and advise on optimization tactics.
By working with specialist OEMs, parts and consumables developers, and industry bodies, wind turbine operators can benefit from industry-leading tools, research and expertise that it would not be cost-effective to build in-house. Through knowledge-sharing, consultancy and close collaboration, operators can draw on this expertise to achieve measurable efficiencies, cost savings and improved return on investment for their equipment, consumables and specialist personnel.
Dr. Rob Profilet is product application specialist, industrial oils, Americas, for Shell. With an undergraduate degree and Ph.D in chemistry, he began his career in industrial lubricants at Texaco in 1993 as a product development chemist. He held various roles in product development, product management and industrial marketing for Equilon and Shell from 1998 to 2006. After eight years at Lubrizol as their global commercial manager for hydraulics, Profilet started his current role at Shell in 2014. He focuses primarily on turbines and next-generation technology.
This piece is excerpted from “Investing in Peak Performance – Strategies for Maximizing Wind-Turbine Operations to Boost Competitive Edge,” published by Shell and completed with insights and contribution from DNV GL and WindEurope. Click here to download the full white paper.