The U.S. government has laid out an ambitious plan to deploy 30 GW of offshore wind power by 2030. After years of impressive progress, offshore wind is ramping up to full commercial maturity and is now becoming a major contributor to energy production. The U.S. alone has an offshore wind power potential of 2,000 GW – double the nation’s current total electricity use.
Floating wind is an emerging technology with a great future. It gives access to abundant wind resources over deep water. Fixed turbines are generally limited to locations about 200 feet deep; because about 80% of offshore wind resources are located in water deeper than that, these new wind resources will be an important addition to an energy mix that will help us to meet emissions targets.
An innovator in floating turbines
aerodyn engineering gmbh, headquartered in Büdelsdorf, Germany, was founded in 1997 to commercialize all patents of physicist and current general manager Sönke Siegfriedsen. Siegfriedsen has worked on the development of turbines since the early 1980s and, in that time, has built strong technical expertise. He now partners with his customers to design innovative wind turbine generators and develop them to market maturity. One of these projects is nezzy2, a turbine installed on a floating foundation.
aerodyn engineering began working on the concept in 2014. During that time, various tests were needed for implementation, as well as extensive research and new calculation methods. For this purpose, aerodyn engineering constructed models at scales of 1:200, 1:36, and 1:10.
Each wind turbine of the 1:10 nezzy2 twin-rotor design can generate 7.5 MW. In 2020, aerodyne engineering and partner EnBW (Energie Baden-Württemberg) tested nezzy2 in a lake and then in the open ocean in northern Germany.
Easier assessment of seaworthiness
To further increase the efficiency of the entire system, aerodyn engineering attaches two wind turbine generators tensioned against each other on the platform at the same time. The seabed of nezzy2 has concrete weights that hold the hull of the turbine – a half-submerged structure – at the end of the weather arm with six anchor chains. This structure forms the floating foundation of the turbine.
The foundation is manufactured from pre-tensioned, precast concrete parts that form a horizontal y-shape. The floating foundation aligns itself automatically using the wind current. Unlike onshore turbine systems, the individual nacelles do not rotate on nezzy2. Instead, the entire above-sea system rotates around a mooring bearing installed in the weather arm.
The two towers rest upon the foundation, set up at an angle and connected to each other and the foundation by anchoring cables. There are currently three-bladed rotors turning, while alternative two-bladed rotors are still waiting to be tested.
The system is completed by large yellow floats, which ensure the stable floating position of the entire structure on the water surface.
Now that the prototype has proved its suitability, aerodyn engineering is currently building the first system in China in the final size.
Although the test turbine in northern Germany is smaller by a factor of 10, that does not mean that it is less complex. The small nezzy2 matches the power and functional scope of the 1:1 version. Its smaller size merely makes it easier to assess the turbine’s seaworthiness.
Synchronous regulation of the turbines
New system concepts also require new methods in automation. The particular challenge with the nezzy2 concept is the synchronous operation of two turbines and the parallel control. In the application at 1:10 scale, the PROFINET network includes a PROFINET controller installed in the measurement station and two PROFINET devices: one installed in the pitch box and one in the inverter.
For the control technology, Siegfriedsen chose the AXC F 2152 from the open PLCnext Technology ecosystem of Phoenix Contact. The AXC F 2152 can be parameterized both as a PROFINET controller and device. This allows up to eight PROFINET devices to be integrated into the network.
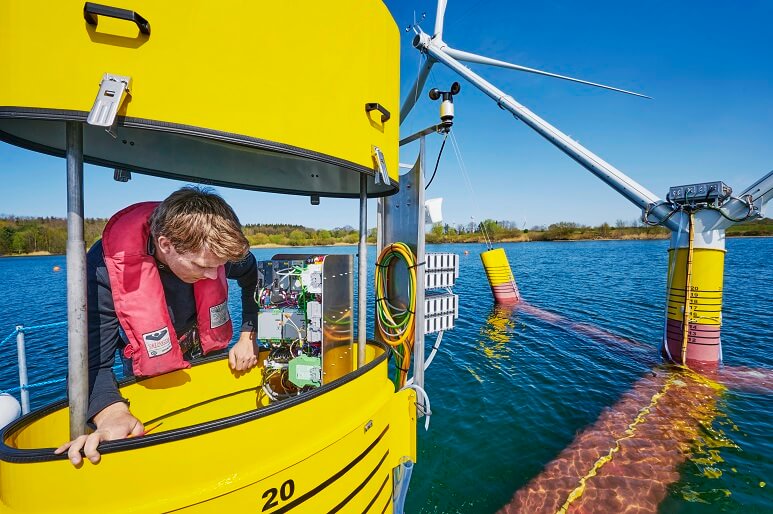
For optimal operation, the two turbines need to be controlled and monitored synchronously. Because of this, engineers decided on two completely identical systems for the design. These systems run completely synchronously in the parameterization. As a result, each of the two turbines has its own automation system with corresponding performance. With a specially developed web visualization, the turbine can be represented as a power station for the user. nezzy2 consists of two autonomously functioning wind turbine generators, which can be viewed as one system.
Continuous remote monitoring
To enable remote control of the complex system, nezzy2 is equipped with a data collector. Approximately 400 data points are queried at 10-millisecond intervals and processed synchronously. Another AXC F 2152 controller collects and exports this data volume.
The controller also ensures communication with the FL mGuard security appliance, which then forwards the data to the remote monitoring system. mGuard devices are robust security components that include firewall, routing and VPN functions for protection against cyber attacks and unwanted malfunctions. The continuous remote monitoring enables ideal monitoring of the wind turbine generator and allows the parameterization to be optimized as needed.
The high number of data points results from the fact that two turbines are being monitored at the same time. The special tensioned design also makes checks necessary in short intervals. For continuous monitoring of loads on the tensioning cables and foundation, numerous sensors are installed in the nezzy2 system. The data collector also collects and transmits this data to the remote control center for monitoring.
Fast adaptation to new requirements
As mentioned above, aerodyn engineering uses the PLCnext Technology controllers for the main control system and the pitch and the data collector. The devices combine the safety and reliability of the traditional PLC world with the openness and flexibility of intelligent components. PLCnext controllers offer the real-time performance and data consistency typical of PLCs, even for high-level languages and model-based code.
Siegfriedsen is also confident that open-source software, apps, and future technologies can be easily integrated into the controllers. Available PLCs can be adapted quickly to changing conditions. Also, the direct cloud connection of the AXC F 2152 ensures that data no longer needs to be stored and analyzed “on the edge.”
In addition, PLCnext Technology enables fast application development, as multiple employees can work on a project at the same time independently of one another in different programming languages.
The PLCnext Technology ecosystem also includes optional safety expansion modules, which make safety-related operations possible. In the nezzy2 project, this means that the entire safety chain is integrated into the control system via controller- and network-independent SafetyBridge Technology. An additional safety controller is not necessary.
The development team faced many challenges in the implementation of the nezzy2 project that PLCnext Technology helped to resolve successfully. The floating wind turbine generator proved its practical suitability and can now be moved to series production.
If the prototype in the original size proves itself, in the future, the innovative turbines might be found next to traditional offshore turbines in the ocean. The floating foundation will create the potential for wind power in new locations that were previously impossible due to water depth.
Carsten Schröder is product manager – wind power at Phoenix Contact Electronics GmbH, and Heinrich Dyck is senior business development manager – wind at Phoenix Contact USA.