The transition to clean energy is at the top of the news agenda, and in recent years, there has been an increase in the number and size of projects for offshore and floating wind across the globe. Countries are racing to transition to a greener future, and floating wind will be a large part of that.
The industry is on the brink of rapid growth and is expected to swell from 74 MW to 126 MW by the end of 2021, according to a recent study from the Floating Wind Joint Industry Project (JIP).
In fact, the idea for large-scale offshore floating wind turbines was first proposed back in the early 1970s. Fast-forward a few decades, and the U.K. has constructed the world’s largest wind farm, Kincardine, and in the U.S., Maine submitted an application for the nation’s first floating offshore wind farm.
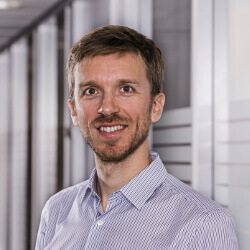
As we progress into the next evolution of offshore wind technology, there are still significant technical challenges the industry faces to achieve large-scale deployment of floating offshore wind.
Here, we will take a closer look at the top five technical impediments to deploying floating offshore wind power at scale (in no particular order).
1. Materials need to be suitable for different markets and site conditions
Floating wind turbine designs cover a wide variety of factors, such as strength, flexibility, flotation and temperature regulation, and need to be suitable to meet a variety of conditions. Conventional offshore wind turbines are installed directly on the seabed and are usually closer to the shore where they may not capture as much wind.
The industry is moving further offshore and into deeper waters to capture the strongest winds. This requires different technology and materials, as floating offshore turbines are held in place by anchoring them to the seabed.
While floating offshore wind’s popularity is growing, there are still challenges in floating wind designs. In fact, it is one of the key topics we discuss during industry events. The power levels for floating wind turbines are expected to reach around 20 MW and will need larger cables for such high voltage levels.
These cables will also need to be designed against any water penetration into the insulation. This requires a water barrier – in steady subsea cables, a lead sheath is usually employed to cover the insulation. However, such a sheath cannot hold out against the dynamic motions of waves and resulting breaking. Using metallic foil and polymer layers can provide more suited protection and solutions for dynamic cables.
2. Installation is complex and time-consuming
Floating wind turbines require dynamic, high-capacity subsea cable systems to collect and export the power generated. High-voltage cables are key elements for floating turbines, as they must move with waves and currents throughout their lifetime and essentially hang from the floater to the seabed. Such cabling has far more movement compared with those attached to the seabed in static offshore wind farms.
The installation of dynamic cables is even more complex than static cables for offshore wind, involving complex operations that need to be performed safely with ultimate control through the installation in order to avoid damages. Specific cable designs and installation methods need to be engineered.
Also, larger vessels and longer installation periods are required to assemble and fit all the accessories needed along the dynamic cables.
3. The evolution of floating wind farms is moving faster than most of the technology
Until now, floating wind farms have primarily been developed as pilot projects with just a few turbines connected together. In such cases, medium-voltage cables are used.
For large-scale commercial projects, there needs to be a higher-voltage export cable. These products have only been used in just two or three projects. The technology is quite innovative and not yet mature. The level of voltage needed for the size of projects that the industry wants to achieve has not yet been used or been qualified by any manufacturer to date.
Similarly, while it may not be a technical hurdle, substations are an important factor, as they will need to be floating as well. The substation offshore will need to be connected to the substation onshore with the export cable. This is something that has been used for the oil and gas industry but now needs to be brought to a larger scale for floating wind.
4. Maintenance, monitoring and inspection
The maintenance of floating offshore wind farms is a complex issue, and there are no one-size-fits-all solutions for monitoring and inspection. While use of the digital twin method or unmanned vessels are useful techniques, advancement in both the gathering of data and its usage is still needed to inform and operate assets.
Heavy maintenance may be required every 10 years, which involves disconnecting and bringing wind turbines to port instead of sending a heavy vessel. As intensive as the process can sound, floating wind turbines can actually reduce the cost of installation and maintenance, as a large part of the turbines can be assembled on land and towed out to the anchor point instead of being built on site. And for maintenance, floating turbines can be towed to shore for repairs.
5. Grid reliability
Several large interconnection projects have been undertaken in recent years, and more are planned in the coming decade. The adoption of these projects, combined with climate pledges, will imply major changes in the energy mix and present significant technical challenges for power grids.
To solve these challenges, ongoing R&D is focused on increasing the reliability as well as the transmission capacity of submarine power cables.
Maxime Toulotte is head of technical marketing for the subsea and land systems business group at Nexans.
Photo: The Hywind Scotland floating offshore wind project. By Øyvind Gravås/Woldcam – Equinor ASA